A revolutionary packaging technology has been developed by Swiss and Portuguese cheese manufacturers to advance the dairy industry across the globe.
A high-tech tray sealer and thermoformer from packaging specialist SEALPAC support these organizations’ objectives.
The European Union has the world’s largest annual consumption of cheese. Manufacturers are competing for the consumer’s hand with their own specialty products Regardless of whether it is a small craft company with a regional customer base or a large-scale cheese producer for export markets. Suitable and innovative packaging is crucial to ensure cheese specialties are of high quality and to ensure their quality on their way to the end user, as well as to stand out from the competition.
The packaging expert SEALPAC has adapted its traysealers and thermoformers to meet the demands of the dairy segment and offers producers innovative packaging solutions that combine optimal product protection with efficient production, simplify logistics, and offer attractive presentations while consuming fewer consumables. SEALPAC helps cheese manufacturers throughout Europe and beyond with the right packaging solutions for distributing and marketing their products.
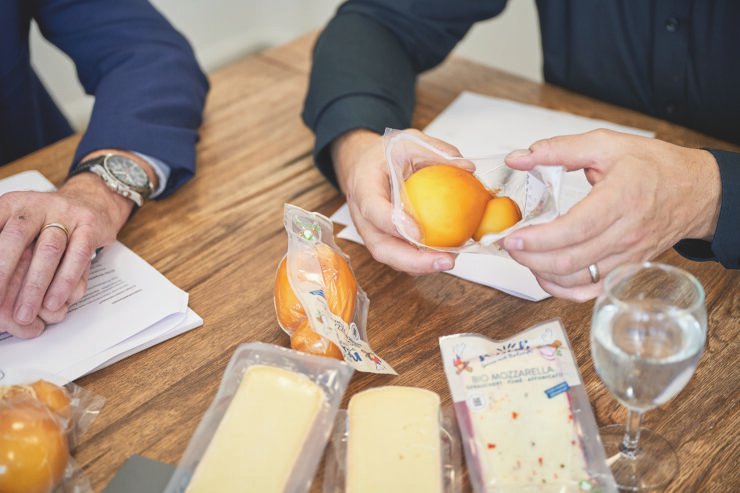
PRO thermoformer from SEALPAC is a compact thermoformer that is tailored to small and medium-sized companies. The space-saving PRO uses consumables and energy extremely economically, and has a modular design. The PRO thermoformer is equipped with an innovative tooling quick exchange system, which reduces changeover times.
The basic PRO machine is suitable for running flexible and rigid film, both for vacuum packaging and sealing-only applications. Different modules can be added to run other packaging solutions, such as MAP, skin, or shrink packaging. The model is the most ideal for the artisan cheese factory.
CEO Roland Rüegg at Wildberg Käserei said, “With the new PRO thermoformer, the pieces of cheese are now packaged from a reel of highly transparent bottom film using Rapid Air Forming. The machine reliably manages particularly thin film that is easy to print, for example with product information, an organic label, or a brand logo.
Besides ensuring consistent high quality, the new thermoformer also makes progress in terms of sustainability: unlike the previous bag solution, thinner films are now used, which saves plastic and reduces storage space.